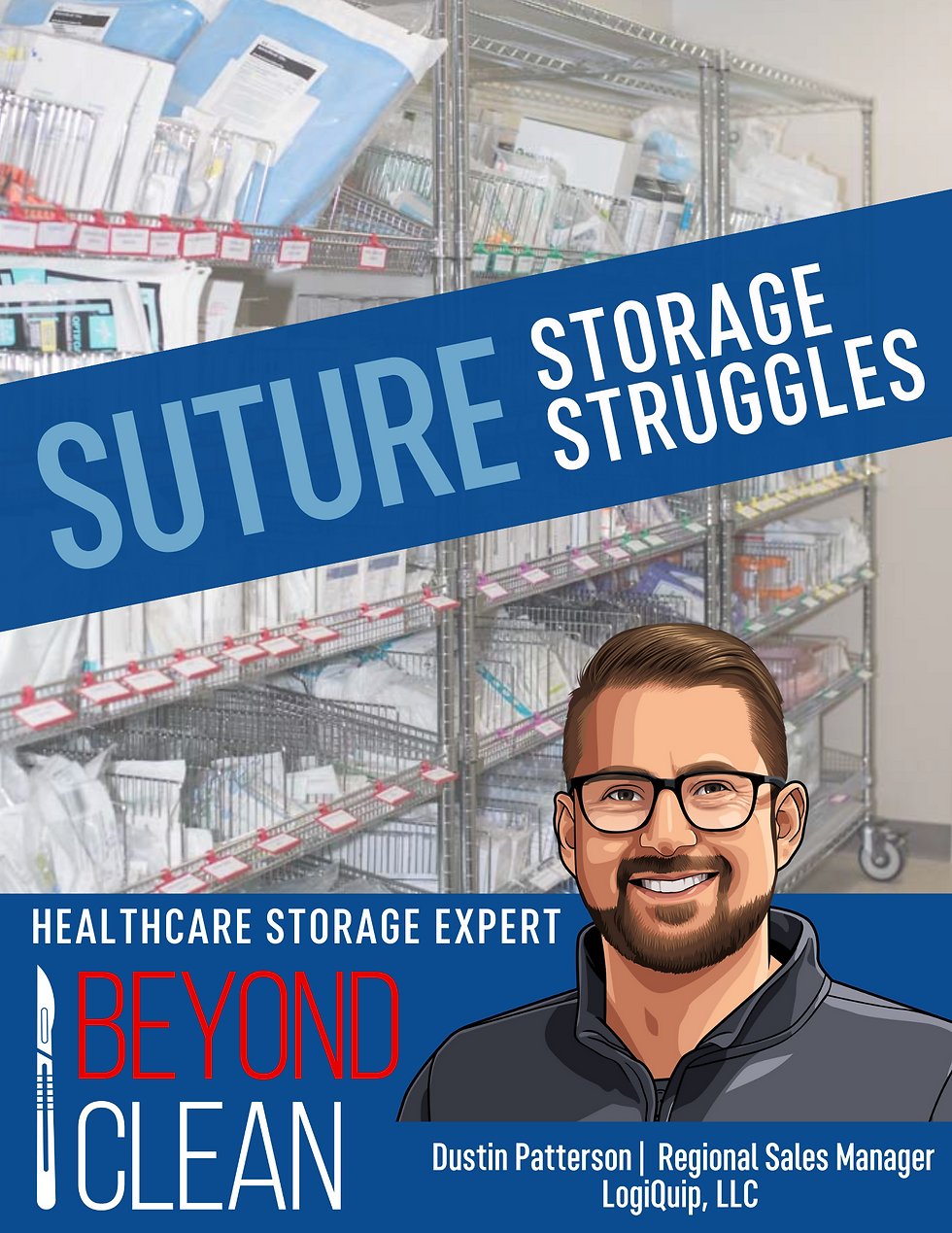
Anybody who works in Sterile Processing can tell you that suture storage is tricky. There is often no standardization, no set PAR Levels, packaging sizes are constantly changing, and no process to manage suture inventory. Any combination of these issues ultimately causes your suture storage area to become inefficient and disorganized.
There are tactics that can be leveraged to better manage suture storage that support FIFO (first in, first out) and reduce waste.
Set your suture bins to 4’’ x 4’’ wide: Suture boxes typically come in a 4'' x 2'' rectangle or 4'' x 4'' square. If you set your lanes to the larger size, you can more easily accommodate the size changes when they happen.
Leverage a two-bin system: With suture boxes frequently changing size you can standardize the location size by eliminating the boxes altogether. Create a two-bin system using traditional plastic bins or fine mesh basket shelving and dividers. Remove the sutures from the boxes, place them in the bins, and label the bin location with a color code (that matches the box) and suture name. We have even adhered the front of the suture box to the bin location, making the sutures you need easier to find.
Set PAR (Periodic Automatic Replenishment) Levels: To do this, you will need to track inventory usage over a period of time to set the minimum and the maximum number of units needed for every suture used. Without set PAR Levels, you may have too few of a high moving suture or too many of a slow-moving suture, potentially causing you to lose sight of expiration dates.
By leveraging one or all the above tactics, your suture storage area will become more efficient and organized.
Kaiser OTC benefits provide members with discounts on over-the-counter medications, vitamins, and health essentials, promoting better health management and cost-effective wellness solutions.
Obituaries near me help you find recent death notices, providing information about funeral services, memorials, and tributes for loved ones in your area.
is traveluro legit? Many users have had mixed experiences with the platform, so it's important to read reviews and verify deals before booking.