SPD’s and Busy Bees: Measuring Productivity in Sterile Processing
- Hank Balch
- Aug 27, 2022
- 4 min read
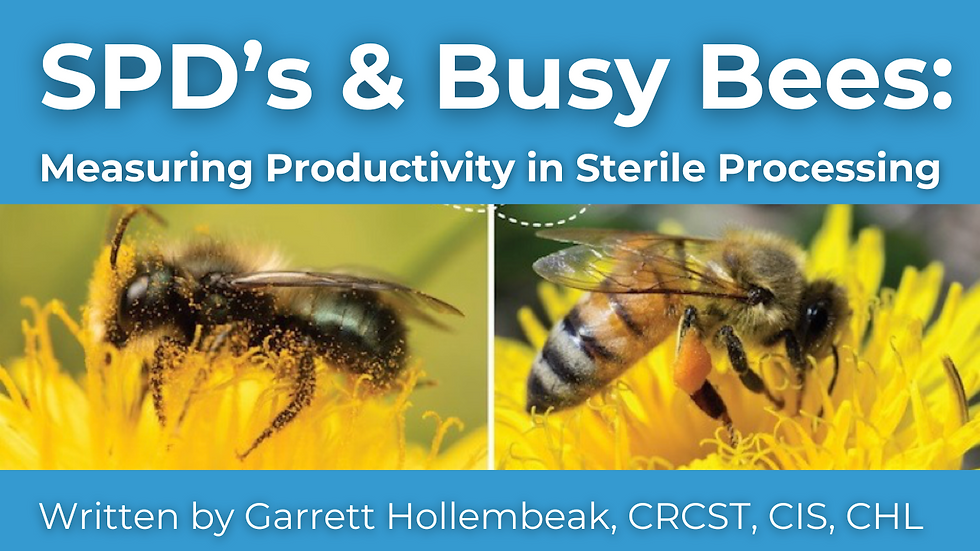
How do we measure productivity in sterile processing? It’s a question that presents a unique challenge for our industry. We expect sterile processing professionals to be fast, thorough, detailed enough to not miss any bioburden, but efficient enough to keep up with the workload. It’s a constant balancing act of quality and quantity. In some departments, the pursuit of productivity has resulted in micromanagement, wacky incentive programs, and benchmarks disconnected from patient safety. In others, management has done away with quantitative metrics, instead relying on their perspective of technicians to gauge their value. In an area of healthcare saturated with standards, sterile processing is unfortunately without many guidelines on how to creatively, comprehensively, and consistently measure productivity. For this we need to step away from the autoclaves and look to nature.
What you see above is a picture of two different bees. Both are workers and both contribute to their fields. The bee on the right is the garden variety honey bee that we all know and love. Honey bees contribute as a tireless member of an integrated team, much like sterile processing professionals. The bee on the left is called a Mason bee. A much less well known member of the bee family with no cereal endorsements and no hive. If that Mason bee were a sterile processing professional and you were to measure their productivity by the amount of honey produced, the Mason bee would appear to be very lazy. A leader in SPD may call that worker into the office and ask them why they struggle to “produce”. Over time this may demoralize the worker and leave them feeling under-appreciated and disengaged.
However, Mason bees are 120x more effective pollinators than honey bees. Their presence in an ecosystem has a tremendous impact on the ability of the honey bees to do their job. Without the Mason bee pollinating so well, it is unlikely that flowers would flourish well enough to support any honey bee hives. In our departments, we can’t expect to have well rounded and dynamic technicians if we don’t also have well rounded and dynamic metrics for productivity. For us to flourish, sterile processing professionals must be evaluated on the value produced.
The challenge for leaders is to understand the work well enough to measure the value that is added. This starts with the value stream of an instrument during reprocessing. We tend to isolate productivity to the activities of cleaning in decontamination, assembling the sets, loading the sterilizers, and building case carts. We could call those the “Honey Bee” activities. However, those are only four of the process steps. There are additional steps that include loading, unloading, returning instruments, completing rework, transporting items, restocking, running to the OR, allocating cases, and a multitude of other elements. These represent labor that not only need to be performed, but are also a challenge to capture. We can call these the “Mason Bee” activities. To ignore or fail to track these ancillary activities gives only a partial picture of our department needs and the contribution of our team.
Another aspect of the value stream comes from looking at the cost associated with those things not being done. With OR time ranging from $60 a minute to $270 a minute, depending on the surgeon and staff in the room, it is easy to see the skyrocketing cost of trays not getting to the operating room in a timely fashion. However, there are also costs that come during the course of production. Chief among these is any time technicians are taken away from their standard productive activities. In the words of Thomas Sowell, “There are no solutions, there are only trade-offs”. For sterile processing, there is a two-fold cost to any activity; the cost of what they are doing, and the “traded-off” cost of what they weren’t able to do in that time.
So let’s take two different technicians. One is a honey bee type worker and spends no time away from their assembly station. We may look at that tech and their high numbers and even set our benchmarks around them. The second tech is a Mason bee worker who steps away from their assembly station every time the instrument washer needs to be unloaded. Their numbers may suffer, but they have contributed to the value stream of the department. The instrument washer had to be emptied, and because the second tech was taking care of that responsibility, the first tech was able to be more productive. As leaders, we have to understand that the second tech’s productivity was actually whatever the first tech got done in the time they would have spent away from their assembly station. To start thinking this way will change the way our teams view priorities in the workflow.
This is a mentality shift for leadership in sterile processing. Fighting microscopic organisms day in and day out can cause our focus to become microscopic as well. It is important for us to zoom out and see the big picture. The forest instead of the trees, or the field instead of the flowers. If we have all pollinators and no honey bees, we have nothing to deliver to our patients. If we have no pollinators, we limit continuous flow. Each technician represents one part of the whole, and we can’t cause one member to be disengaged without eroding the productivity of the entire department. Recognition is a primary factor in engagement, and organizations with robust employee engagement programs are 14% more productive than those that don’t (Valarie Daunt Partner - Consulting, 2014).
Taking the time to praise and recognize the Mason bees and the honey bees will help them feel seen, heard, and respected. Add to that the benefit of less burnout and reduced absenteeism. Sterile processing professionals are some of the hardest working, industrious, and buzzworthy (pun intended) out there. Creatively, comprehensively, and consistently measuring productivity for all types of workers honors the impact of our industry and the life-changing, life-saving contribution of our sterile processing professionals.
-Garrett Hollembeak, CRCST, CIS, CHL
Sterile Processing & Distribution Manager
Sources:
PDX parent. PDX Parent. (2022, August 24). Retrieved August 27, 2022, from https://pdxparent.com/
Authors Valarie Daunt Partner - Consulting vdaunt@deloitte.ie +353 1 417 8633 . (2014, August 20). Recognition programmes – are they important?: Deloitte Ireland: Deloitte Private. Deloitte Ireland. Retrieved August 27, 2022, from https://www2.deloitte.com/ie/en/pages/deloitte-private/articles/recognition-programmes.html
Goodreads. (n.d.). A conflict of visions quotes by Thomas Sowell. Goodreads. Retrieved August 27, 2022, from https://www.goodreads.com/work/quotes/6913-a-conflict-of-visions-ideological-origins-of-political-struggles
コメント